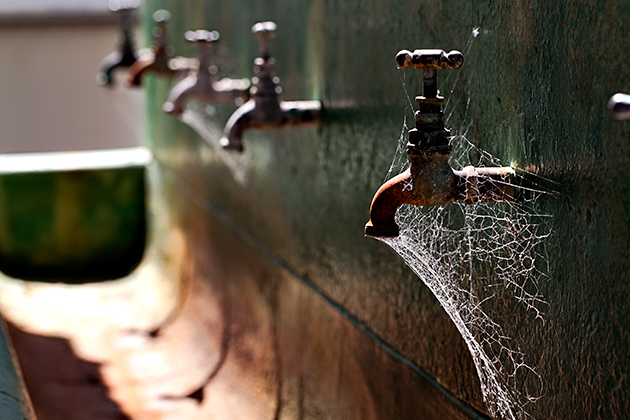
Water does not generate the respect or anxiety it deserves. While floods and droughts may get considerable attention, another, perhaps more critical threat is much more subtle: the lack of available water to meet growing demand. If current trends persist, global water demand will increase by 55% between 2000 and 2050. Some industries’ requirements will soar even higher—by 140% for electricity production and 400% for manufacturing.
Recognition of these critical water-related challenges is also increasing. In Pacific Institute and Vox Global’s 2014 survey “Bridging Concern With Action: Are U.S. Companies Prepared for Looming Water Challenges?” nearly 60% of more than 50 major corporations indicated that water issues are worsening and could negatively affect their business growth and profitability within five years. More than 80% said water availability will influence decisions on where to locate facilities.
The CDP Global Water Report 2013 reveals similar concerns among 180 companies listed on the FTSE Global 500 Equity Index. Analysis by CDP (formerly the Carbon Disclosure Project) shows that water issues can threaten profitability and shareholder security. Some 70% of companies stated that water presents substantive business risks and half have experienced detrimental business impacts related to water since 2009.
Water risks are increasingly immediate, especially in direct operations and supply chains. Insufficient or inadequate water supply or a lack of infrastructure to reliably deliver that supply can all affect production volume and quality. In CDP’s analysis, the most widely-identified near-term risks were water stress or scarcity, flooding, rising compliance costs, declining water quality, higher water prices and reputational damage caused by growing public and media awareness of water issues and companies’ handling thereof.
Reducing water use and increasing re-use are important, but potential water shortages are not the only major risk-driver. It is essential to require key suppliers to measure and manage their own water risks. Nearly a quarter of companies in CDP’s analysis do not know if water presents a risk to their supply chains and, in the Pacific Institute survey, few respondents reported any plans to expand their water risk mitigation measures. According to CDP, this low level of strategic planning or corporate ambition on key water stewardship metrics increases the risk. Fortunately, however, some proactive companies are exploring more effective water management strategies and have developed ways to address water efficiency, savings and reliability.
Spotting Opportunities and Risks
The first step businesses should take is to assess their water risk and exposure by regularly measuring and monitoring water use to determine its value to the operation. “Water’s full value is much greater than its procurement costs, which are normally fairly low,” said Lauren Koopman, a director in PwC’s Sustainable Business Solutions practice. “Its indirect costs include treatment, transport, supplier engagement, and risk of community or NGO backlash. Rising water consciousness is creating a ripple effect through the supply chain.” For instance, retailers sourcing water near Texas drought areas have experienced lower production, which has negatively affected profits and sales.
The costs of water acquisition and disposal are familiar considerations. For example, manufacturer Cummins Inc. developed an internal statistical model “to identify the least efficient facilities, where the greatest conservation opportunities exist, based on size, number of employees and type of work,” said Todd Swingle, the company’s director of environmental strategy. He visited 20 Cummins sites in 2013 to perform an extensive water audit as part of an effort to understand all direct water-related costs and the “water/energy nexus.”
“Many of our projects have both water and energy improvements,” Swingle said. “For water projects, look beyond purchase and disposal costs to maintenance, expenses of pumping and moving greater volumes of water, and chemical costs of having to treat more water, requiring larger machines and more energy. Calculating all the factors to assess real costs of water use could lead to far greater savings than initially obvious.”
Other companies have instituted policies to better monitor and manage water use. At United Technologies, any location spending more than $100,000 a year on energy and water is required to report its water use every quarter. “Then we evaluate reports from over 400 facilities to see if they’re on target to reduce their water use to meet our goal of 40% reduction for 2015,” said Rick Love, manager of environmental sustainability.
Many risk assessment tools are available to help water management efforts. “You can use them for macroscopic assessment of your sites, then prioritize the sites you need to focus on,” said Philip Sumner, senior manager in Pfizer’s GTS Global Engineering. “Do local assessments to identify specific opportunities. Water management is a quickly-evolving area, with a lot of new data becoming available. It needs constant review.
“Our top priority regarding water risks is supply reliability and quantity. Water quality and flooding are next, followed by access. Access may be one step from our immediate operations, but the opportunities are there,” he said.
Formulating a water strategy involves gauging operational disruptions, quality issues, physical impacts, and regulatory or reputational factors. Any new player entering a watershed affects all users. “We’re seeing increased disclosure about the current state and quantity of water usage to comply with local regulations,” Koopman said. “Greater efficiency can raise production quantity with limited water supply. Ask, ‘Which initiatives could mitigate problems? How do we bring the greatest value at the lowest environmental impact?’”
When the Hershey Company evaluated each of its plants, “we had a sense of how much water was coming in or going out, but weren’t always sure of what happened to water in between,” said Todd Camp, senior director for corporate social responsibility and community relations. A thorough analysis of each facility’s entire water footprint conducted by their environmental and engineering departments in conjunction with outside water experts pointed leadership toward the biggest opportunities to make an impact, and those which require capital.
To set goals, Hershey considers climate change and the potential for water stress in its operating areas, as well as expert predictions of future local water shortages. “We look at ROI for capital investment for all environmental projects,” Camp said. “Thanks to senior management support, we’re often allowed leeway for a longer-than-normal payback period for something in line with our environmental stewardship commitment.”

Pursuing Water Improvements
After gaining an understanding of water’s value and the related risks, companies often discover adjustments are necessary to better address their needs. Some changes are as basic as storing water when it is available and conserving it when it is less available, Koopman said.
Sometimes water conservation can require a little creativity. “We’ve had success with rainwater recapture, and with re-using HVAC water condensate,” Sumner said. “It accumulates on the outsides of large air-conditioning units, is very clean, and can be caught in drip pans. If you have any steam systems, look into capturing steam condensate; it’s pure hot water to re-use.”
Typically, he seeks out cost-avoidance measures, explaining, “If you need more water, that might take a new treatment system, which does require capital, depending on that facility’s footprint.” Finding ways to re-use water
can be cheaper, however. A big challenge, Sumner cautions, is the low cost of water. “It’s been so inexpensive that implementing water-saving projects can be difficult to justify from the cost-savings perspective.”
It is also important to understand how the water quality being delivered by a local utility affects operations. “We try to focus on conservation opportunities, regulations regarding discharging, and where risks exist concerning water availability and quality,” Swingle said. “Much of water management is making risks and opportunities visible. We have to highlight the business value, such as risks and possible impact of water supply interruptions in water-scarce areas. Where we already know the water utility is not reliable, we may need storage tanks of at least one day’s supply, should the utility not deliver. In an emerging market, that utility could be down for days. A U.S. utility facing water restrictions might ask us to cut back by a defined amount, and we [need to be able] to do that readily.”
Even within a single worksite, there may be different water quality needs. “Energy comes in, gets used by a machine, then disappears or turns into heat,” Swingle said. “Water also enters many machines. It may leave as wastewater, requiring processing, or re-enter as treated water. When you buy water from a utility, the quality may be fine for many purposes, but certain sensitive kinds of equipment, such as boilers, could require higher-purity water, meaning you’ll have to treat it again before use. When looking for opportunities to reduce water use, risks are often hidden. Knowing what you’re looking for is part of water’s complexity.”
At Hershey, after the engineering department determines which techniques would be most effective without impairing the manufacturing quality, the company holds an education campaign for all employees. Methodical long-term pilot projects for every particular process confirm modifications that allow each plant to harness new water-related technologies.
At its largest plant, Hershey considered many environmental factors to plan the site’s expansion. “Water was a key factor in redesigning our proprietary technology,” Camp said. “We took the opportunity to upgrade our heating and cooling.” Water efficiency analysis even included faucets in the cafeterias and they now reuse water in a closed-loop system. More efficient heating and cooling towers maintain previous output while reducing the company’s water footprint significantly.
Hershey’s greatest water use is in its manufacturing process, which requires careful cleaning. “Water and chocolate don’t always play nice together,” Camp said. Different zones in each plant require varying temperature and humidity levels to protect product quality and appearance. “Moving through the cooling tunnel is like going from Minnesota to Miami, so that’s where most of our water efficiency is needed,” he explained.
United Technologies has several facilities in Singapore, a city-state deeply concerned about water and its availability. “It’s a robust, growing economy, but Singapore is small and reliant on neighboring countries,” Love said. The government decided to re-pipe Singapore, especially in its industrial areas, in an ambitious water re-use and recycling program called NEWater.
“At one time, our Singapore sites had a single set of pipes containing potable water. The NEWater system uses two sets of pipes, so now we have access to potable water where you need it, such as for drinking, and non-potable water for things like cooling,” Love said. He is pleased that, by adding chemicals to the water used for certain manufacturing processes, that water will remain reusable for cooling. “The Republic of Singapore has dramatically reduced its water use, and we’re saving about 15 million gallons per year over the previous year. This also helps Singapore and our neighbors.”
At its location in West Palm Beach, Florida, United Technologies must cope with the area’s serious water problems, including scarcity and saltwater entering the aquifer. In their jet engine and helicopter plants, employees took several steps to reduce the amount of water used on-site. “Just installing low-flow sink aerators for hand-washing lowered our water use from 2.2 gallons per minute to 0.5 gallons,” Love said.
Even though pipelines need to be flushed more often in Florida than in cooler climates, the company was able to reduce water use in its plating shops. Increasing thermostat settings to make the air conditioning two degrees warmer lessened the load on cooling towers, for example. Like Camp, Love endorses employee engagement. United Technologies trained South Florida employees about water sensitivity and reporting starting with the policy that, “if you see a leak, tell someone.” “By 2013, all the changes reduced our water use by 30 million gallons from 2006. We exceeded our 40% goal [for water use reduction],” Love said.
A Group Effort
Collective action in stressed regions is becoming increasingly common. “There’s growing realization that more can be done by working with other groups.” Koopman said. “In water-stressed regions, companies are collaborating with other companies, governments, NGOs and local communities to address water issues that affect all parties. We see companies that are direct competitors working together to secure water supply in scarce regions.”
In many locations, Koopman also sees tightening water standards. “You’ll have to understand and comply with new regulations,” she said. “That’s easier when you understand your water use. Some companies send questionnaires to local facility managers who are on the ground and understand water issues that may affect those sites.”
For on-site visits, Swingle sometimes brings Cummins environmental leaders with some prior water experience. “It’s also an opportunity to educate resource people in some water-related nuances, compared to other environmental areas. Having a large staff that focuses on water isn’t practical, but we need people to understand enough about it to recognize challenges and opportunities.” In seeking possible water use reductions, risks are often hidden. “Knowing what you’re looking for is the challenge. Consultants can do that; we’ve used them to extend our reach, or in a very specialized area.”
In areas with greater risk exposure, companies should design facilities and manufacturing processes that, ideally, will need little or no water to operate. “For instance, where water is scarce, choose air-cooled rather than water-cooled air conditioning (although that does use more energy),” Swingle said. “Understand which equipment is dependent on water, and make choices to mitigate. Assign an expected risk value to each project. Have an emergency plan in place, covering possible local responses.” Facilities and manufacturing staff can often identify viable water-saving solutions as well. “The key is to conduct this evaluation before the emergency occurs.”
“Water sounds so easy,” Sumner added, “but there’s a lot to it. That’s why it’s such an exciting field.”