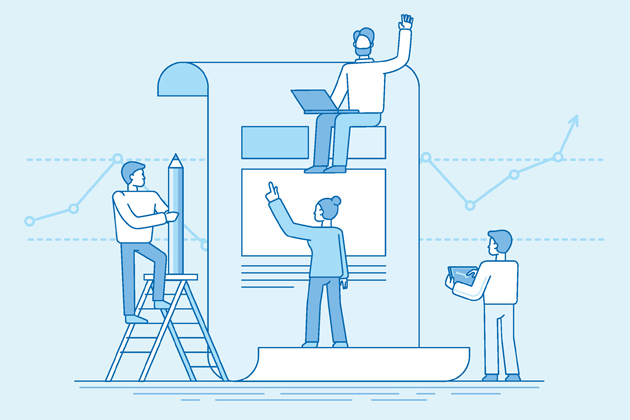
Construction defect issues can be complex and costly to resolve. Common problems include water intrusion through windows, walls and roofs, noise transfer through common walls, foundation cracks from geotechnical conditions, questionable structural integrity, and interior moisture management. Each warrants close attention to not only fix, but also to identify what caused the problem and who should bear the costs of repair, whether that is builders, project owners, end users or insurance companies.
The importance of minimizing defects in construction cannot be over-emphasized. The old adage “an ounce of prevention is worth a pound of cure” is particularly apt. Fixing a potential problem at the pre-construction stage may cost only $100 of an architect’s or draftsman’s time. Fixing that same problem due to unclear or misleading plan details during construction could cost $1,000, plus scheduling delays. Ignoring the problem until water intrusion, dry rot or fire occurs may cost $1 million or more to repair, depending on the extent of damage, and could even result in injury or death. Therefore, focusing on quality assurance can improve your performance and avoid costly claims.
Addressing the following seven areas can provide builders with additional guidance to help ensure the highest quality work:
1. Organizational Structure
Rather than report to the field construction team, the builder’s quality assurance representative or customer service team members should report up through a different chain of command, such as the company’s sales and marketing or warranty department. This eliminates the risk of having the “fox guarding the hen house” and empowers an independent senior manager outside the construction circle to stop a project if quality falls below standards of care.
2. Evaluation of Trade Contractors
Rigorous evaluations of trade contractors are essential to ensure high-quality workmanship and product durability. Fundamentally, this is what project sponsors, investors, homebuyers and renters expect. A trade contractor’s experience with specific building types is vital. For instance, those constructing a high-rise building need experience with high-rises, not just single-family, wood-framed structures. Fellow contractor and trade references are also important, as are insurance and safety documentation from other active projects. Knowing the financial strength of contractors and other vendors, as well as the size and scale of their operations, are all key factors to help avoid working with entities that could be overextended.
3. Project Delivery Tools
It is important to thoroughly detail the plans, specs and trade scopes-of-work, tailor them to the design and price range for the specific product being constructed, and use the latest software technology available throughout the construction process.
If the project plans lack details for acoustical assemblies or window flashing installations, for example, the trade contractors may invent their own solutions, resulting in a compromised component and lower level of performance. Specification manuals can provide a conceptual “recipe book” for projects to be built, while mock-ups near the project site create a laboratory “test-kitchen” experience for installers of new or unfamiliar products, and training on 3-D installation sequences.
Information management systems can assist with tracking plan changes, managing the project’s paper flow, and creating useful as-built archives. These systems are particularly important when a revolving door of trade contractors may be cycling through a given project, and are helpful in verifying the quality oversight built into the project should a construction defect claim arise well after project completion.
4. Bonuses and Incentives
Construction managers, field superintendents and trade contractors should be trained and incentivized to look at a project’s lifespan beyond the current status of construction. Successful projects have useful lives spanning decades. How do contractors motivate their field teams to think long-term? Cash bonuses earned and accrued over the span of a certain phase or the life of a project, but not yet paid, could be deposited in the superintendent’s bonus pool. These funds held by the company can ultimately be paid out once quality objectives are realized.
5. Balancing Competing Interests
Schedules, costs and quality are three equally vital factors in the production delivery process, but can often come into conflict. Some manufacturers have been successful in balancing these interests, however. One case in point is the Toyota Production System (TPS), an integrated socio-technical system of management philosophy and practices for improvement processes. As part of TPS, workers on an assembly line can stop production in real time if a flaw or problem is discovered, and then develop a solution right where the problem originated. A similar production methodology can be applied to construction projects by establishing “job-ready/job-complete” standards that require a trade contractor’s sign-off on a prior trade’s workmanship before beginning their own work.
6. Responsive Customer Service
Managing customer expectations is key throughout the entire construction process, beginning with sales, continuing through the development process and then through the warranty period and beyond. Providing many customer service “touch points” throughout the construction and delivery processes can build strong relationships between builders and their buyers, minimizing risks of litigation.
7. Third-Party Peer Reviews
Third-party peer review and quality assurance should encompass the full project delivery life cycle. In the pre-construction phase, peer reviews of architectural and engineering plans, specification manuals and trade scopes can help avoid later problems.
During construction, peer review observation, documentation and classification of key litigation-generating assemblies (such as windows) is critical for managing construction defect risk. The key is to discover and proactively correct those hidden flaws before installation of any components that cover up preceding work, such as roofing or wall assemblies.
Post-construction considerations include preparation of comprehensive maintenance manuals to help building owners and community managers understand their fiduciary responsibilities from the start of construction through their period of ownership.