Until last year, most companies regarded energy bills as simply a cost of doing business—and often a relatively low cost at that. While efforts to reduce energy use or move to renewable sources may have been part of a long-term sustainability drive, few companies thought that there was any urgent need to transition quickly. All that changed, however, when Russia turned off Europe’s gas supply in response to sanctions imposed following the country’s invasion of Ukraine.
Before March 2022, the European Union imported almost 40% of its natural gas from Russia, with Germany being the largest importer by volume. Now, that supply has stopped and European gas prices for delivery in 2023 and 2024 have more than doubled, and costs are expected to remain high moving forward.
Businesses are feeling the strain and many have been forced to adapt quickly, often losing money in the process. German viscose fiber maker Kelheim Fibres, which supplies consumer goods giant Procter & Gamble, cut output twice at its factory before winter hit. It has switched from gas to heating oil and is considering moving to hydrogen, as well as setting up a two-megawatt solar power plant to meet future energy needs. Tata Chemicals, which formerly operated on a five-year plan, started working on a quarterly basis last year due to the problems of sourcing energy and materials in Europe. Meanwhile, Luxembourg-based steel maker ArcelorMittal is set to cut production at two German plants following better-than-expected performance at a facility in Texas, where gas prices are much cheaper and more stable. Volkswagen is also expanding its operations in the Unites States, while carmaker Tesla paused plans to produce batteries in Germany. In the United Kingdom, one in eight manufacturers surveyed by business association Make UK had to make job cuts in 2022 as a direct result of increased energy bills, with some considering site shutdowns to survive.
The situation in Europe serves as a reminder to companies everywhere that even in key and stable markets, energy supplies can be disrupted, increasing operational costs and risks as a result. Such energy shortages can force production to slow down, shift to other countries or halt altogether. They can also prompt customers to source goods and services from suppliers in other markets. Furthermore, energy disruption is likely to become an increasingly frequent—and potentially critical—risk. Demand for electrical energy production is set to double by 2035, which may also bring price hikes, shortages and outages.
Higher energy costs can also lead to legal risks. Not only could delays in production and shipping trigger breach of contract claims from customers and suppliers, but there is a risk that executives could be held personally liable for failing to inform the market or regulators about the financial impact that energy price increases or supply chain disruption might have on the business. “The effect of high energy prices on a company is material, especially where local laws and/or listing rules compel them to not trade while insolvent and to not mislead markets as to the company’s true financial state,” said John Zadkovich, partner at law firm Penningtons Manches Cooper.
Searching for Simple Solutions
Companies need to reconsider both the impact of energy risk in the short-term, as well as how they might become more energy resilient in the long-term. Luckily, experts say reducing current energy use and expenditure can be done quickly, at little cost and little effort. The key is to conduct an energy audit to know how much energy the company is using, where the most energy-intensive parts of their operations are, and what machinery and equipment could be categorized as non-critical and could be switched off.
Most energy providers can engage with commercial measurement services (at varying prices) and the assessment can enable an immediate understanding of energy-hungry processes and systems. Some companies may also be able to do their own assessments of how energy-intensive some processes are if they are using new IoT-enabled technology that provides real-time reporting of energy usage. Once the organization understands how energy is used, it can then look at operational efficiencies. In fact, it may be amazed by how much energy it actually wastes.
For example, Scott Armstrong, the chief operating officer of sustainability consultancy Planet Mark, conducted an onsite energy audit for a hotel group several years ago. He noticed there was a spike in energy use in the kitchen between 4 a.m. and 6 a.m. every day—some two hours before breakfast prep started. It turned out the chef asked the night cleaner to switch all the equipment on early so that the ovens would already be at the right temperature when he began work at 6 a.m. The night cleaner got a free bacon sandwich for his help, while the hotel got an additional £20,000 energy bill per year. “Operational impacts on energy management can have a huge impact on your bottom line,” he said.
Checks like this can provide simple solutions. Adrian Guggisberg, president of motion services at engineering firm ABB, said there is so much low-hanging fruit that companies do not need to make drastic changes or massive investments in new technologies to realize immediate cost savings through cuts in energy consumption. Guggisberg believes most organizations can secure a 20% to 30% reduction in energy consumption through changes in behavior and equipment. For example, around 10% of global electrical energy production could be saved if industries used more efficient motors.
Simple but effective energy efficiency measures can include using LED lighting with motion/daylight sensors and properly insulating roofs and walls. Together, these measures can slash bills in half. In factories, manufacturers could look at ways to reuse waste heat to power other processes. They could also examine whether it is worth moving machinery closer together as poor factory layout can increase the time it takes to do even basic tasks (which increases production costs) and also cost more to heat.
“Just looking at the data about where your energy use is highest will tell you where you can make cuts,” Guggisberg said. “A lot of companies assume that temperatures in factories or offices need to be constant all the time. They don’t—they just shouldn’t fluctuate wildly. Similarly, equipment and machinery should be turned off when not in use to reduce power usage. You do not need to make expensive changes to see positive results.”
Companies should not make any substantial investment in new energy-efficient equipment until they have found ways to cut costs using existing equipment first. “There is no point replacing old equipment with new IoT-based technology while continuing to operate in the same way,” Guggisberg said. “You have to operate more intelligently. Many companies still do not even know where their energy use is highest because, up until now, few cared—energy bills were simply a cost of doing business. But now that energy prices have soared, companies need to become more energy efficient. The temptation is to invest in new equipment, but looking at operational processes and how energy is used will probably yield significant savings in the immediate term. Only after companies understand how they are using energy, and how they can use it more efficiently, should they consider making any significant investments in new technologies and other equipment.”
Enhancing Enterprise Efficiency
While small, immediate changes can yield significant results, companies should regard energy and fuel price increases as a catalyst to “consider energy efficient and sustainable alternatives to help manage business costs while also reducing emissions and carbon footprint,” said Laura Capper, head of manufacturing and construction at Ulster Bank in the U.K.
She believes companies should strive for “material efficiency” as well as “energy efficiency.” To do this, companies should consider whether they can negotiate cheaper material costs or source cheaper materials that will do a similar job. Reducing the amount of material in some products or designing new products with less material and eliminating some product features can also help cut manufacturing and energy costs. Reusing materials is also an option.
Keeping material and inventory levels low may also reduce costs, she said, while buying materials that are already made to specification may help reduce onsite production costs and cut energy use. Preventing overproduction and minimizing product inventory so completed goods are shipped off premises as fast as possible can also reduce storage costs and speed up sales.
Company culture has a key part to play in the journey. “Ensure team members understand why there is a need to be more efficient and encourage them to suggest ideas that will save energy, materials and time,” Capper said. Setting priority areas and targets, showing the benefits the changes have caused, and recognizing and celebrating success can all be powerful ways of encouraging team involvement. Setting goals to lower energy consumption is another way to get the workforce actively involved.
Other actions can include developing energy “hedging” strategies. Rob Morgan, head of energy at procurement consultancy 4C Associates, said companies “should look at contracting forward for energy and other potentially impacted commodities to protect against price spikes and supply reductions.” Another option is to hedge against future energy price hikes by using commodity futures, though this requires a detailed understanding and monitoring of the instruments used.
According to Chris Bowden, managing director of clean energy firm Squeaky, companies can also look at using corporate power purchase agreements (CPPA), which are long-term contracts between an energy buyer and an energy generator to buy and sell renewable energy at an agreed price, usually over a period of 10 to 15 years. This helps businesses buy energy at below wholesale market prices and lock in a long-term supply of clean energy. A CPPA can also help organizations trace their energy supply to verify its environmental impact, reduce their indirect supply chain (Scope 3) emissions, and accelerate their net-zero journey.
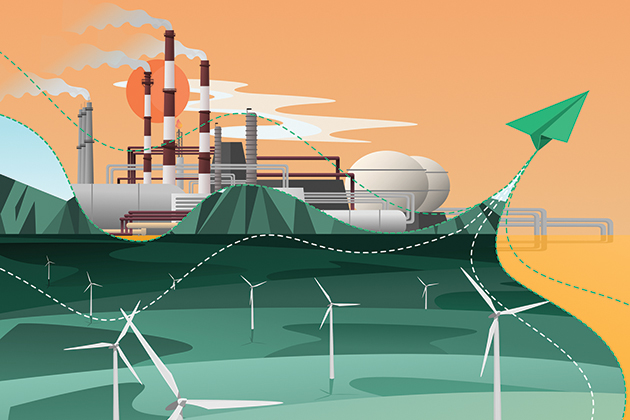
Looking Longer Term
As part of longer-term efforts to mitigate future energy risks, companies should review their risk registers to see how exposed they could be to potential energy shocks. This requires updating crisis management plans and keeping informed about geopolitical developments in energy-producing and mineral-rich regions. Energy-intensive companies in particular should ensure they follow oil, gas and power prices closely and pursue strategies that are in line with their own exposure, risk appetite and market position. More generally, companies should review the steps they are taking to better understand the potential direct and indirect impacts of energy shortages on key customers and suppliers. They could also consider using price escalation clauses to pass prices on to customers, or directly procuring energy the moment a sale is agreed upon.
Additionally, companies need to question the potential impacts of energy risks on their strategy and the bottom line, and then consider how they may need to adapt their objectives in response. Organizations should also think about how they can use their investor relations, communications and policy teams to inform stakeholders (including regulators) about how their operations, strategy and financials have been impacted by energy risks.
Organizations should also connect the risk management and risk monitoring teams across their enterprise and provide a forum to allow different functions to discuss their energy risks to understand how they stack up when viewed as a single risk scenario that could impact future energy needs. Similarly, according to Al Adedeyo, energy lead partner for operational transformation at KPMG, “Key customers, along with Tier 1 and 2 suppliers, should be engaged with increased levels of trust and transparency to encourage them to provide early warning signals that a problem is on the horizon that could impact them and, in turn, your company.”
To ensure energy resilience, Adedeyo recommended that companies focus on escalating the frequency and depth of their reviews of supply chain resilience metrics (such as inventories) and stress-test critical supply chains under various energy supply scenarios. He also suggested developing a communications plan for customers that can be put into action in the event of a disruption, as well as building inventories of finished products for priority customers so that supply is not disrupted in the event of a power outage or rationing.
According to consultancy McKinsey, the most significant mid- to long-term opportunity to mitigate high energy costs comes from plans that energy-intensive users already have in place. Most large companies, for example, have adopted decarbonization strategies that typically involve reducing energy consumption by around 50% over the next decade. This is especially the case in Europe due to sustainability rules. Implementing a big part of those changes in two to three years would not only mitigate the currently expected price increases, but also could create a real competitive advantage. The main barriers to success are organizational, not technical or financial. As a result, most companies in most industries should be able to follow and adopt these efforts.
Improving Energy Resilience
Ultimately, companies need to look at sourcing from renewable energy, as well as generating and/or reusing energy themselves. Wind and solar are the most frequent forms of energy that companies are generating on their own, and doing so is becoming increasingly popular and manageable. For example, Swedish furniture retailer IKEA has 935,000 solar panels on the roofs of its stores and warehouses. Other possibilities include installing micro-hydropower systems and using biomass energy from wood logs, chips, bark and sawdust. However, these options require capital investments that might be outside the reach of some companies.
Nevertheless, the rewards are likely to outstrip the initial pain of paying up-front. Apart from lower energy bills, there are several benefits of transitioning to renewable energy and generating it on the premises. First, energy costs and supply are more predictable. Since business operations are no longer subject to fluctuating oil and gas prices or geopolitical instability, companies can better forecast their expenses and supply. Second, business continuity can be improved as operations are less likely to be disrupted by an electricity outage. Third, companies can improve their brand image by going green, which may offer some competitive advantages. Finally, switching to renewables can create an additional income stream if the company sells surplus wind or solar energy back to the grid for a profit.
Experts believe that all companies need to start moving toward better energy risk management and energy resilience and that organizations should incorporate these efforts into their sustainability programs. Some are already making the move. For example, Mercedes-Benz has said Europe’s gas crisis will act as a catalyst for the company to push into renewables. It has announced the construction of an on-site wind farm that will eventually provide more than 15% of its electricity needs across Germany and has also signed on to use a wind energy facility in the Baltic Sea that will add another 25% of capacity. However, for the most part, “there is still a lag between companies recognizing the risk and responding to it,” Guggisberg said. “Currently, energy risk management is principally driven by fear rather than sustainability.”
With the Russia-Ukraine crisis still ongoing, Skyler Chi, global head of enterprise accounts at governance, risk and compliance solutions provider Exiger, said companies need to take a more serious look at the issues of energy independence and consider alternatives like onshoring or “friend shoring,” meaning sourcing goods, materials and services from politically friendly and stable countries.
“U.S. companies are more focused on energy risk mitigation and price volatility than looking at long-term energy independence,” he said. “They see energy risk as a cost issue rather than a long-term sustainability problem. The situation with Russia and Ukraine should serve as a warning about how reliant companies have become on foreign energy supplies, both directly and indirectly. Even if companies are not based in countries that are reliant on Russian gas, you can bet their suppliers are dependent on it.”