
Every year, slips, trips and falls are a leading cause of workplace injuries. According to the 2018 Liberty Mutual Insurance Workplace Safety Index, U.S. businesses paid more than $11 billion in 2015 (the most recent year for which data was available) in direct workers compensation costs for slips, trips and falls, and that does not even include the costs of liability or lost productivity.
In fact, same-level falls were the second most costly cause of workplace injuries after overexertion, accounting for more than 19% of all injury cases, while slips and trips without falls ranked seventh, accounting for almost 4% of injuries and another $2 billion in costs. Additionally, the National Safety Council (NSC) reports that nearly 30% of same-level falls result in more than 21 lost workdays per incident—a heavy blow to the many companies that are already facing a shortage of skilled workers.
Despite the obvious risk, the recent Walk Zone Safety report by New Pig, a manufacturer of products to minimize workplace hazards, found that more than half of the maintenance and safety professionals surveyed do not consider same-level fall prevention a top priority, even though 42% confirmed at least one same-level fall in their workplace in the past year and a significant number had more than five falls.
Uncovering the Real Causes
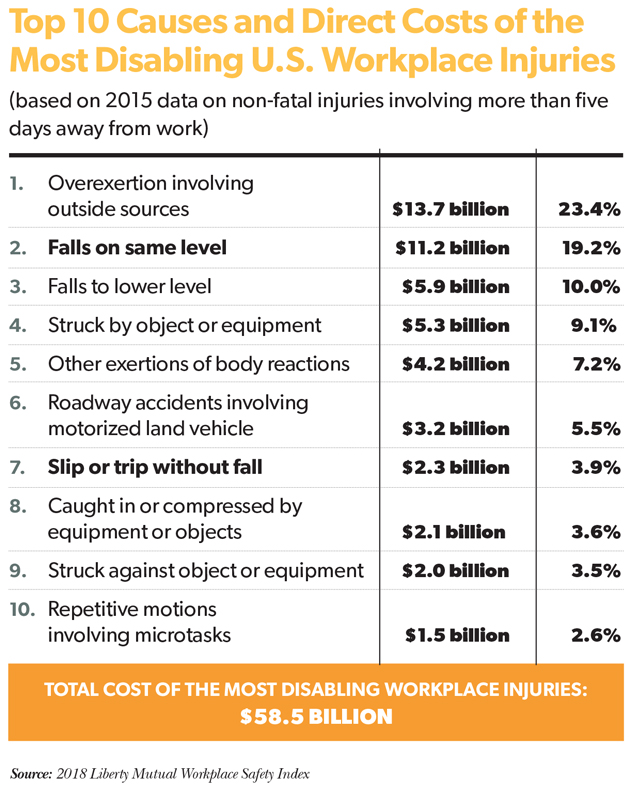
When ranking floor safety efforts in order of importance, however, respondents to the Walk Zone Safety survey, put “providing safe walking surfaces” last, behind “requiring appropriate footwear” and “safety training.” Almost a quarter indicated they leave floor safety in the hands of their rental mat vendor or cleaning contractor. In short, the study found that, despite the high cost and even higher risk, preventing same-level falls is a low priority.
In addition to understanding how the condition of the floor surface contributes to same-level slips and falls, it is also essential to recognize the areas most prone to accidents. For example, while 92% of survey respondents reported placing mats in entranceways, only 31% use them in transition areas.
Conducting a Slip and Fall Audit
To minimize slip and fall accidents in industrial environments, the first step is conducting an audit of all walkways, high-traffic and transition areas, as well as housekeeping procedures and maintenance measures. Knowing where the risks are can help companies focus attention on the real problem areas. Incident reports and workers compensation claims can also help identify previous trouble spots and their causes.
Keep in mind, this audit should be used as part of a larger slip and fall prevention plan that goes beyond same-level incidents. Such evaluation should also be conducted throughout a project or work cycle during a daily walk-around.
Assess entrance, high-traffic and transition areas. Most facilities and buildings have an entrance mat to absorb rain, snow, mud and grime tracked in from outside. The problem is that many companies “set them and forget them.” Over time, these rugs and mats become dirty, shift position, wear down, and wrinkle or crease. Regular maintenance of the rug and floor surface is critical.
Consider the proper amount of walk-off space when using entrance mats. An eight- to 10-foot walk-off area inside the door—enough for someone to take six steps—is considered a best practice. Other high-risk and underserved areas should also be addressed, including the floor space around water fountains, frequently-used machines or any equipment that processes liquids.
Depending upon the kind of work being done, there could be additional hazard areas due to material on the floor (dust, shavings, liquids), heat or temperature changes that could make a floor slippery, or grime brought in from outside equipment. Reviewing each of these areas and the factors that could contribute to slips or falls will help with prioritizing a plan.
Check permanent and temporary stairways for potential issues. According to OSHA, stairway treads and walkways should always be free of dangerous objects, debris and materials. Slippery conditions on stairways and walkways must be addressed immediately. Stairways with four or more risers or those that rise more than 30 inches need to have at least one handrail.
Review maintenance and housekeeping procedures. Problems with improper cleaning procedures can result from both over-cleaning and under-cleaning. When the floor is not cleaned frequently enough, dirt can build up and cause the surface to become slippery. On the other hand, using the wrong cleaning solution or over-cleaning certain areas can damage the floor’s finish, which helps to maintain friction and prevent falls. Following the floor manufacturer’s directions for cleaning is highly recommended to avoid these potential issues.
The timing of cleanings is also important. Schedule floor-washing during times with the least amount of foot traffic to ensure the surface is thoroughly cleaned and able to dry before frequent use resumes. Keep in mind that more slips and falls happen during the winter months and on rainy days, so it is also a good idea to plan maintenance schedules around weather events to minimize hazards.
Review hazard communication signs and procedures. Be sure to clearly and effectively communicate potential slip and fall hazards through the appropriate signage if the hazards cannot be immediately corrected. Assign one person or a group of team members to place signs around potentially hazardous zones daily to prevent unnecessary accidents. Employees should also be briefed on the dangers of distracted walking to reduce the potential for accidents.
Assess use and placement of tools and materials during shifts. Make note of improper placement of tools, cables and other items that could lead to hazardous trips. All too often, slip and fall accidents are the last link in a chain of mistakes. Once notes are compiled, review them as part of the audit to identify the root cause of the problem and look for alternatives to having items on the floor. Often, companies will even be able to identify a specific employee or team that is not following procedures correctly.
It is also important to note that many industries have specific standards for protecting workers against slip and fall hazards. Be sure to add any information or procedures that align with industry guidelines to the audit list as needed.
Developing a Written Floor Safety Program
There are several factors to consider when addressing floor safety risks and creating a comprehensive plan to reduce same-level slips, trips and falls, which should be documented in the form of written guidelines that clearly identify hazards and state how your company plans to protect employees from slip and fall hazards.
First, determine who is responsible for maintenance. Some companies prefer to have a contractor, facility manager or vendor handle the care and cleaning of their floors and floor mats. While that may work for some facilities, it may not be a logical option for others because it removes a measure of control. A floor safety program that is developed, owned and managed by the company itself may be more effective because the company will be more driven to make it successful.
Next, use a planogram to map out the placement of fall-prevention mats in main and secondary entrances, high-traffic areas, and areas identified during the audit where loose or uncontained materials (oil, dust, water) could make the floor slippery. Consider custom-sized mats for the intended area. Multiple issues can arise when mats are too small or too large for the surface. Adhesive-backed mats that can be cut to size are a safer alternative to traditional carpeted mats that can shift, ripple and buckle. Look for mats that also absorb moisture and dirt.
A maintenance schedule that includes regular cleaning, audits and internal training should be part of the program. Training employees about hazard identification, avoidance and control will go a long way toward ensuring their safety.
Finally, it is important to consider the human element when creating a comprehensive floor safety strategy. Even the best products and procedures may require the buy-in and commitment of employees who understand the rationale behind the program.
Making Prevention a Priority
For decades, the cornerstone of slip and fall prevention has been the quick and easy fix of placing a yellow “wet floor” sign or orange cone in high-risk areas. For those in a hurry, however, the signs likely go unnoticed. If they have been left out permanently due to a chronic issue, the signs or cones may even become virtually invisible.
Committing to a fall-prevention strategy is also committing to avoiding temporary solutions. In the end, a solid plan aimed at reducing slips, trips and falls—coupled with a concerted effort by the entire organization to enforce it—will save time and money and prevent injury.