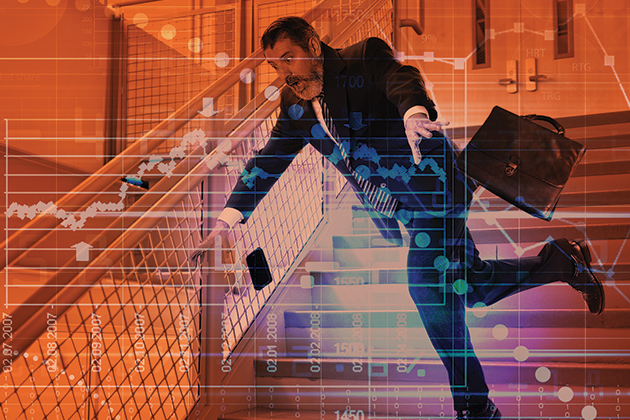
When it comes to building a successful business, employees are the heart of a company. The primary job of employers is to protect their workers and give them a safe environment to come to every day. Preventing workplace injuries, therefore, is one of the main priorities of every organization. Proactive use of devices and data can help companies better achieve this by highlighting areas requiring greater attention to improve safety performance. Combining that with prescriptive analysis to identify actionable insights provides a useful blend of prediction and action to boost safety performance.
Using software to measure a risk-reduction process that identifies, communicates, mitigates and verifies risks can produce leading indicators of performance to improve workplace conditions. While the definition of leading indicators from the U.S. Occupational Safety and Health Administration focuses on variables such as time of actions and number of Management of Change (MOC) training sessions, there is an even more robust set of leading indicators that can be used to help mitigate the potential for an incident.
There are three steps to follow in to order to be successful with a predictive analytics initiative:
1. Create a risk reporting culture.
Creating a process for workers to document incidents and near-misses is as vital as developing a system for management to respond to this reporting appropriately. Today, workers have more ability to report and track incidents and near-misses than ever before. Besides wearables, phone apps allow workers to take photos and fill out forms on the spot. This increases accuracy, as users do not have to rely on memory to complete reports after the fact. That type of quality data feeds the predictive analytics models that help companies determine improvement areas in their workplaces. For instance, one worker at a company reported a deer sighting as a risk. This might sound trivial, but when you consider that there are about 1.5 million deer-related road accidents annually and that deer have been involved in more than 1,000 airplane-related incidents in the United States in the past 10 years, this potential four-hoofed hazard could affect any company that transports goods or equipment in areas where deer are present. Also, had management dismissed that near-miss out of hand, it could have caused that worker and possibly others to stop reporting incidents altogether. Without a culture that promotes reporting by acting upon each reported event, the quantity and quality of the data necessary for true predictive analytics is diminished.
2. Harness quality data.
To perform true predictive analysis, you need data and lots of it. But not just any data; you need quality data. You also need integrated data because, if the various divisions of a company take a “left hand does not know what the right hand is doing” approach to risk mitigation, it is unlikely that helpful analytics will be shared to monitor potential safety problems with similar equipment or situations in different locations.
The good news is that, in today’s business world, there is data everywhere. With the emergence of internet of things (IoT) technology, we can now draw data from our devices and operating equipment in new ways to empower predictive analytics programs to better identify potential risks. Technology allows us to collect terabytes of data that can be sliced in different ways to predict risks, whether it is a sensor that monitors poisonous gases, wearables that keep an eye on workers for signs of fatigue, heat stress or speeding heart rates, or drones hovering over difficult terrain to provide a clearer picture of potential risks without putting workers in harm’s way.
3. Implement a risk-reduction cycle.
The challenge starts with implementing a risk-reduction cycle that improves performance. This requires using the proper tools to allow your workforce to manage the process and measure its execution. Today’s software tools give companies the ability to use leading indicators to track and locate the areas of their business that are most at risk, or are less likely, but still at risk of causing injuries or even fatalities in the workplace. Recent breakthroughs in software capabilities and process standardization have helped transform predictive analytics into a powerful tool that compiles incidents and near-incidents, injuries and even fatalities to determine the areas that should be addressed to keep workers safe.
Predictive analytics in workplace safety can be misconstrued as a “silver bullet” that keeps workers safe. The software is extremely important in mitigating risk, but at the end of the day, data is just that—data. It takes people to mitigate risk. Predictive analytics cannot foretell that, if you are not careful next Tuesday, you are likely to be in an accident, but it can give your workers the information they need to be alert for potential hazards.
Benchmarking with lagging indicators has been around for quite some time. Now, we have the capability to benchmark with leading indicators that have been proven with predictive analytics. Being able to tap into that collective knowledge allows companies to home in on areas that need improvements in process execution as well as performance. It is important to remember, however, that while software may be an invaluable tool to gather the data necessary to generate the predictive analytics needed to improve performance, it still takes human competence to drive change.